私の場合、排気装置の価格や設置サイズの問題でなかなか形状が決定できませんでした。
今回採用を見送りましたが様々なパターンを考えましたので、これから作られる方の参考になればと思います。
パターン1 ネロ式の仕切り板を立てる。
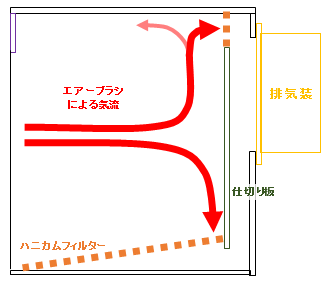
これを見た方は「いままでのネロ式解説意味がないのでは?」と思う方もいると思います。
「パナソニック レンジフード・換気扇」や「スプレーワーク ペインティングブースII」で見られる形です。
ただこの形にするには「排気装置」が「とても強力」である必要があります。
上方に流れた気流をうまく吸引するのがネロ式の利点ですが、排気装置が強力であれば跳ね返りが起こる前に吸えます。
残りはピンクの矢印で跳ね返りを最少に抑える事ができます。
※この形にする場合の注意点として仕切り板を中途半端な角度にしない事。(90~80°まで)
そうしないと上部吸気口が塗装する物と同一線上となり、吹きあがった余計な塗料が落ちて塗装面を汚す原因になります。
この形状の場合ブース内を広くつかえる利点がありますが、排気装置の価格とサイズが上がる事となり不採用としました。
パターン2 排気装置を外部ユニット化する。
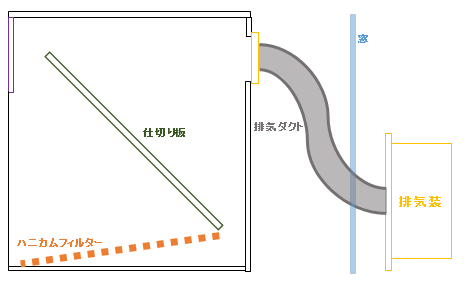
室内のブースサイズが広げられないなら排気装置を外部ユニット化するという考えです。
(図では窓の外ですが換気ダクトの中間に排気装置を設置する場合もあります。)
利点はブースサイズが排気装置のサイズに影響されない。
欠点として屋外設置の場合常設できない。
持ち運びするには重量・サイズの問題がある。
吸入口から排気装置までが距離があり排気能力が落ちる為、ある程度の性能がある排気装置が必要(コスト増)となり不採用としました。
国内メーカのシロッコファンは性能によりφ140、φ150、φ160と種類があります。今回φ140と仮定して
a. ブースに直接換気装置を設置
(ブース排出口)換気扇吸入口φ140→換気扇排出口φ100→排気ダクト排出口φ100
b1. 排気ダクトを通してから換気装置を設置(φ150)
ブース排出口φ150→排気ダクトφ150→換気扇吸入口φ140→排気ダクト排出口φ100
b2. 排気ダクトを通してから換気装置を設置(φ100)
ブース排出口φ100→排気ダクトφ100→換気扇吸入口φ140→排気ダクト排出口φ100
a. b1. の場合はまだ良いのですが、b2.の場合排気ダクトの径が増減する分抵抗が増えてしまいます。
パターン3 排気装置を外部ユニット化する。(ダブルファン)
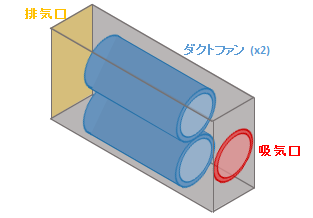
先のパターン2の排気装置をダクトファンx2で設置し吸気効率を上げようとしました。
「25Pa・300m³/h」のファンを並列配置した場合、計算上「25Pa・600m³/h」になるそうです。
(「ファン&ブロア」より)
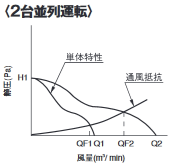
※実際には表面積増大により壁面圧力損失の影響が増える事を考慮しなければなりません。
ただし吸入口(赤色の円)がダクトファンの径面積(青色の円)より大きい必要があり、ダブルファンそのままの径だと意味をなさないそうです。
・ダクトファンφ150x2の場合、φ225以上必要
・ダクトファンφ100x2の場合、φ150以上必要
ダクトファンφ100で手頃な性能の機種が見つからなかったこと、出し入れがサイズ的に面倒なので不採用となりました。
あと基本ダクトファン自体音量が大きい製品が多くそれを外に置くと近所迷惑になる可能性があります。
(ただしBoxを作成するので遮音材などで音を小さくできる可能性はあります。)
換気装置のユニット化に関しては、他にも考えられている方がおらっしゃり
「消音ボックス付多翼ファン」を特許登録されている企業もあります。(効果不明)
パターン4 排気装置を外部ユニット化する。(窓枠設置型)
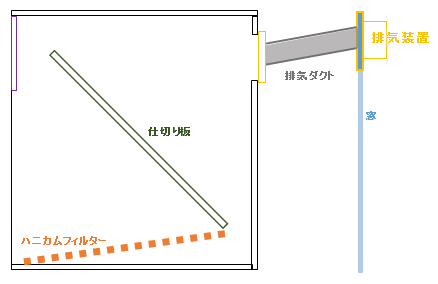
一般的な換気扇を窓枠に設置する形。
この形の欠点は先の例でもある排気ダクトでロスが発生するという事。
例:ブース抵抗を2Pa、ダクト抵抗を8Paで吸引能力が15Paとすると
a. ブース内の抵抗のみの圧力で吸い込まれる
15-2=13Paで吸引できる。排出口では5Pa残る
b. ブース内とダクトの抵抗圧力で吸い込まれる
15-(2+10)=5Paで吸引される。排出口では5Pa残る
結果どうしても排気装置を大型化しなければならずサイズ・重量的に取り外しもできなくなるので不採用としました。
ただハイブリット(吸気側と排気側に排気装置を用意する)にすれば、とても有効かと思います。
「25Pa・300m³/h」のファンを直列配置した場合、計算上1.5倍の「37.5Pa・300m³/h」(専用ファンで1.8~2.0倍の「45Pa~50Pa・300m³/h」)になるそうです。
(「ファン&ブロア」より)

※ ファン自体を重ねて繋いだ場合です。途中でダクト等を使用するとその分圧力損失が生まれます。
例:排気能力が劣るが小さい排気装置をブース側に設置、足りない分を排気側の排気装置で補う。(排気ダクトが長い場合などで有利)
例:排気する場所がない場合、家の換気扇に取り付けれられるようにアダプタを作成。使うときに差し込むようにする。
「トンボ 漬物容器 浅9型」がサイズ的に合うそうです。
(「塗装ブース総合スレッド24」で教えていただきました。ありがとうございます。)
パターン5 跳ね返り防止板を長くする。
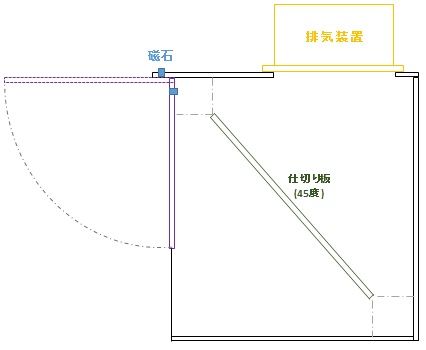
跳ね返り防止板を開閉式にして跳ね返り防止及び吸引力を高める方法。
開けた時は磁石の力で固定すると考えました。
ドラフトチャンバーだとスライド式ですが、構造を簡単にするために前開きで設定してみました。
欠点はやはり作業スペースが狭くなる事となり頻繁に開閉しなければならない事。
跳ね返り防止板による色味の差が気になる事。(汚れる事も想定して)
以上の点を踏まえ不採用としましたが、ブース自体が大型の場合有効になるでしょう。
パターン6 排気装置を斜めに設置する。
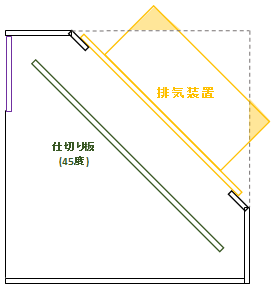
排気装置を斜めに設置する事で省スペースを狙った形です。
懸念点は吸引室が小さいのでどの様に影響がでるか?という所と
メンテナンスの際、シロッコファンを引き抜けるか?という点です。
利点は小スペース化で、斜めにしたことで換気扇面積を広げることができる事です。
また上部下部にある吸入口までの距離が等距離になります。(吸い込みバランスが良い。)
欠点はやはり黄色い三角の部分だけははみ出る事。
加工難易度が若干上がる事です。
今回はそれでもスペースが足りなく不採用となりましたが、もう少しサイズに余裕があれば試したかった形です。
私の場合、「小スペース・移動できる・低コスト」があり上記方式を見送りました。
(ここに書けない案もありました。)
形を検討しては、それに合う換気装置の選定。思っていた商品が無い、価格が高いなどで断念を何度も繰り返しました。
次に「スプレー缶の噴射能力はどのぐらいか?」という内容を記載しておきます。
またエアーブラシでの値も載せておきますので参考にして下さい。